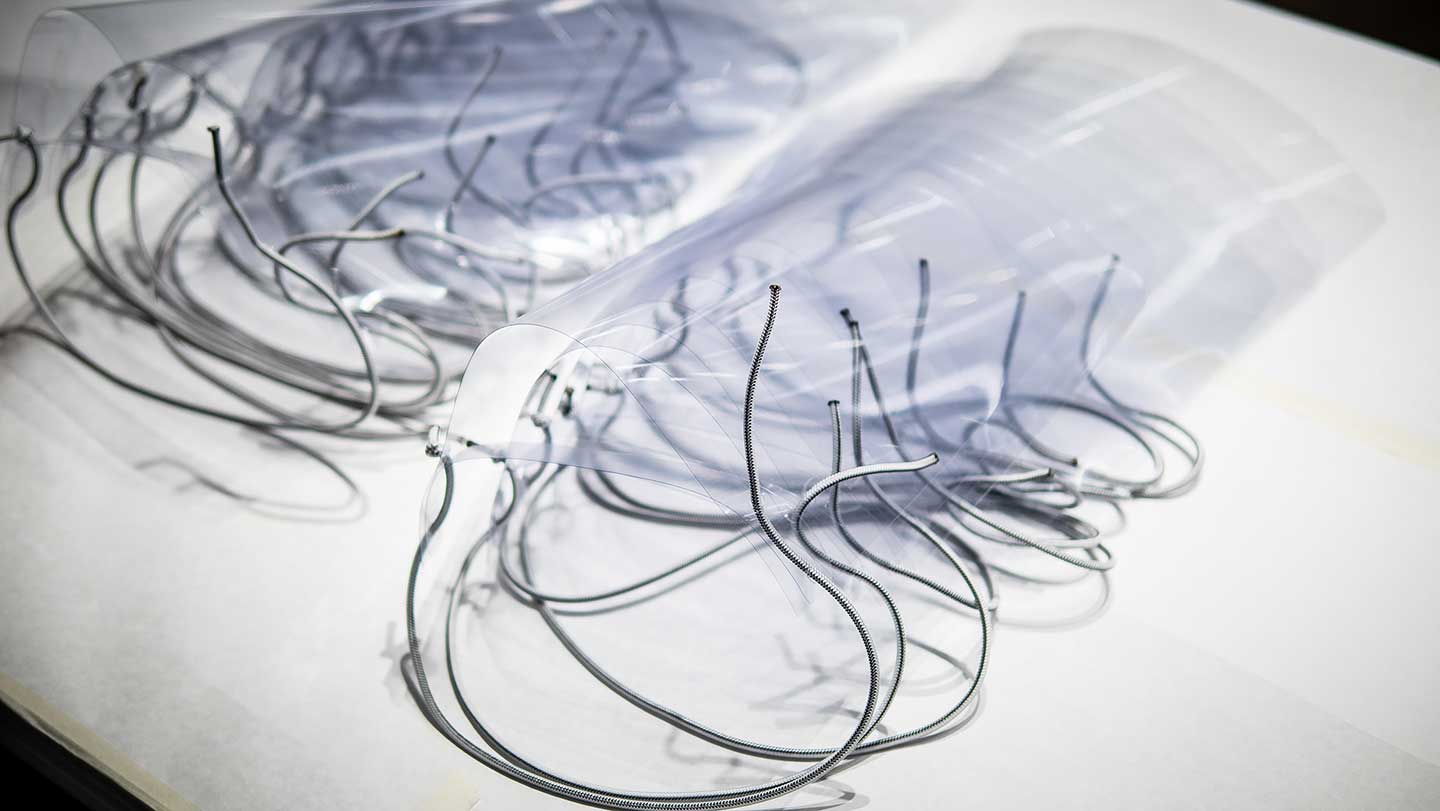
Racing Against Time
Montclair State
MIX Lab delivered
tens of thousands
of face shields
to COVID-19
front line workers
When Montclair State’s MIX Lab team started producing face shields on 3D printers amid the growing COVID-19 pandemic, they quickly realized it wasn’t enough. The team needed to figure out how to make more – and fast.
“The need for PPE (personal protective equipment) is at scale,” says Iain Kerr, co-director with Jason Frasca of the MIX Lab and professor of Innovation Design. Kerr reports that in northern New Jersey alone, the demand is for hundreds of thousands of face shields, if not more.
“The U.S. needs 3.5 billion masks. And this region – the megalopolis from Boston to Washington, D.C. – needs over 200 million shields,” says Kerr. “3D printing 350 a day was not the way to go.”
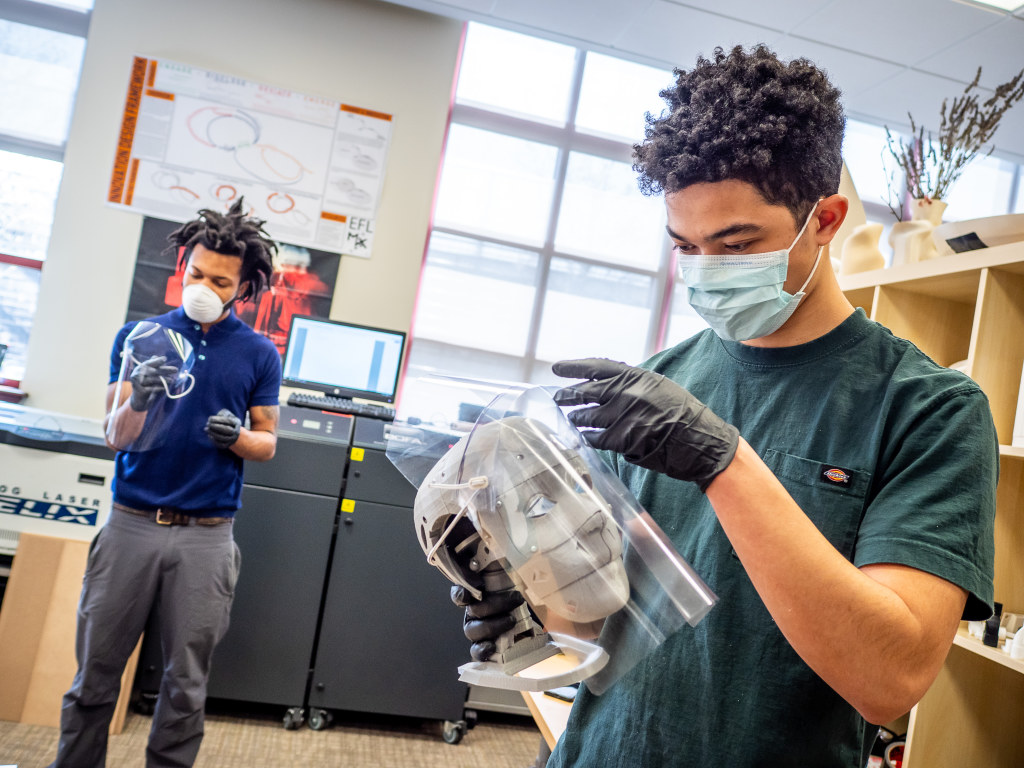
The MIX Lab, founded in 2015 and housed in Montclair State University’s Feliciano Center for Entrepreneurship & Innovation (FCE&I), is a facility where students and community members work together to solve problems using innovation and digitally mediated “making” – aka 3D printing.
To address the need for better design and process in making mass quantities of face shields, the MIX Lab has joined with Montclair Design Week/DesignShed and Michael Rees of William Paterson University. The team is now collaborating on everything from research to design to supply chain management to hospital interface, volunteer recruitment, social media outreach and fundraising.
On the design end, the result of the collaboration is new open-source face shields that can be produced more cheaply (potentially less than $1/unit as compared to more than $5/unit) and faster than those the MIX Lab was 3D printing. “We have two designs, one closed at top and one open,” says Kerr. “They’re both super cheap.”
He says the designs use “very little 3D printing and a ton of ingenuity.”
“You can literally make these face shields with scissors and a hole punch and some binding covers and elastic streamers,” says Altarik Banks ’18, innovation and design researcher for MIX Lab and design principal of the collective design studio HOMA.
Banks credits team member Alex McDonald for many of the improvements. “In terms of production, now we have them cut in a streamline process. There’s a drill press, a jig, a paper cutter,” he says.
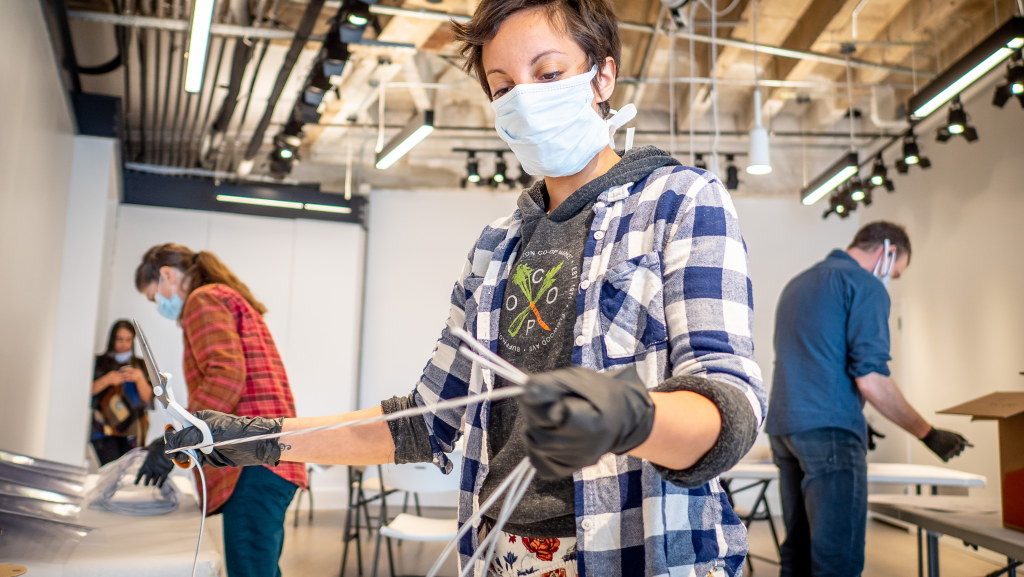
Currently, the team has converted the Montclair Innovation Lab at Lackawanna Plaza into an assembly line where Montclair Design Week is coordinating volunteers. “When the machine works perfectly, we can get over 1,000 shields a day out the door – and they are what the hospitals want,” Kerr says.
“How does a regular person like me help in a pandemic? My support for this effort helped make 1,684 face shields to provide to three hospitals in NJ including the one where me and my siblings were born. It is a great thing to be able to do.”
Meanwhile, the 3D printers have been freed up for specialty projects.
By the end of April, more than 15,000 face shields had been delivered – with more in production – to RWJBarnabas Health System, University Hospital, St. Joseph’s Regional Medical Center in Paterson, Mountainside Hospital, Hackensack University Medical Center Palisades, The Valley Hospital in Ridgewood, and Montclair State University Emergency Medical Services.
The only components needed are more money and more volunteers – and that is changing fast.
“We can fabricate the pieces at 1,500 per hour,” Kerr says. “If we had the materials and we had a volunteer force available, we could be making a huge amount.”
To make that happen, the University has set up a crowdfunding/giving page. In addition, the Feliciano Center reallocated $10,000 in 3D printing supplies no longer needed for educational purposes as a result of the transition to an online delivery model and received $17,000 in donations, 100% of which will be used to purchase materials.
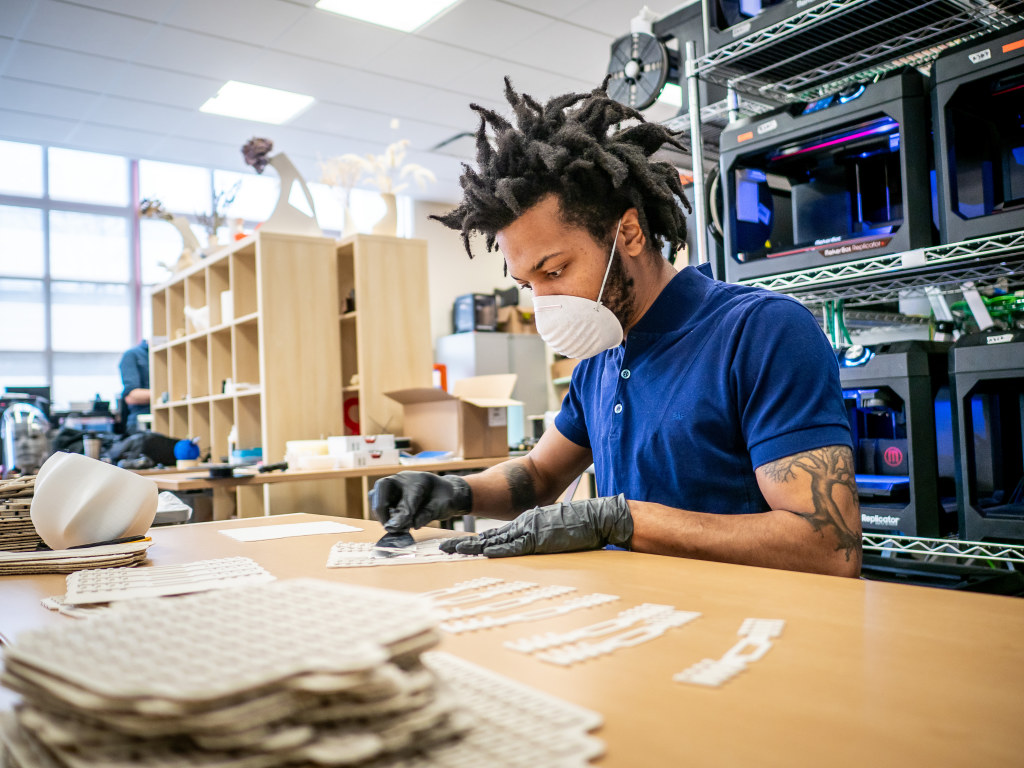
The lab has received generous support from some of the University’s supporters, including The Provident Bank Foundation and alumnus Joe Cucci ’66.
“How does a regular person like me help in a pandemic? My support for this effort helped make 1,684 face shields to provide to three hospitals in New Jersey including the one where me and my siblings were born,” says Cucci. “It is a great thing to be able to do.”
Beyond its own assembly line, the MIX Lab team is working to coordinate the makers’ community across New Jersey utilizing a Facebook page (New Jersey Makers Response to COVID-19).
“We’re trying to get people to switch to this family of designs. It sounds kinda cool to have this 3D high tech method, but if you move to this simpler method, you can make thousands,” says Kerr.
“Part of our mission is to innovate as well as collaborate with others – whether that be the global makers’ community or local higher education,” says Feliciano School of Business Clinical Specialist and MIX Lab Co-Director Jason Frasca. “We want to move people to better, faster designs.”
“Core to the Center’s work is collaboration with a rich ecosystem of global and local talent that helps blur the line between where MSU’s campus ends and where the entrepreneurial community begins,” says FCE&I Executive Director Carley Graham Garcia. “It is this innovation that got noticed by local hospitals and health care providers as COVID-19 began to rapidly spread around the world and in our own backyard.”
Says Banks, “It’s really powerful and really impactful that our product is reaching the front line workers. I’m really excited about it.”